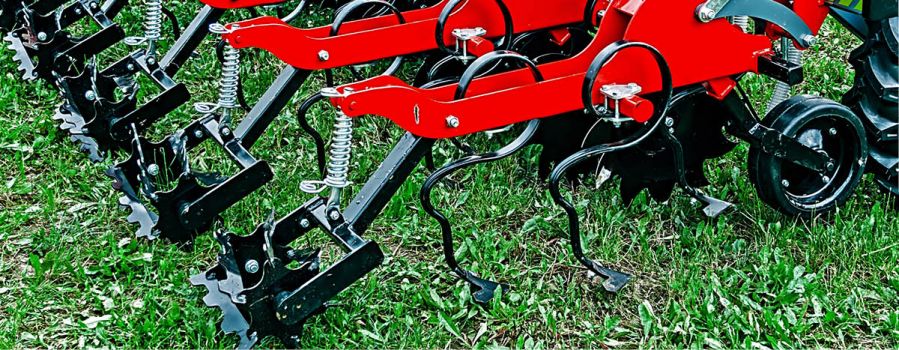
Machinery Costs and Purchases - Are You Improving Your Bottom Line?
Article By: Brad Sirianni
Machinery and equipment costs on farms are a major aspect of the business. Determining how much to invest in it, whether it be repairs or purchases, requires in-depth analysis. FINBIN data from 2019-2023 show that machinery costs per acre and repair costs for dairy and crop farms have steadily increased. The information below will provide insight, raise important questions, and provide resources to help answer any questions.
Repairs costs have been steadily increasing. These costs have been a big factor in declining net farm incomes. Crop farms data is represented by a range of 1,304 to 1,521 farms. Dairy farms are 365-284 farms. *
The graph above shows increasing annual machinery costs per crop per year. The graph also shows the difference in costs by crops. Soybeans have the lowest machinery costs and corn silage have the highest costs per acre. Soybean farms data is represented by a range of 1,811 to 1,915 farms. Corn farms, a range of 1,899-2,017 farms. Alfalfa farms, a range of 408-425 farms. Corn silage farms, a range of 501-561 farms. *
The graph above shows Wisconsin farms have a higher machinery cost per acre versus the average farm. This has been a common trend for many years. There are not many Wisconsin farms represented in the data; however, it could reveal that Wisconsin farms need to evaluate this area. Alfalfa farms data is represented by a range of 408-425 farms. Corn silage farms, a range of 501-561 farms. WI alfalfa farms, a range of 29-56 farms. WI corn silage farm, a range of 29-63. *
The data in the graphs demonstrate the importance of how much value any given purchase or repair brings to the farm operation. It raises questions:
- When do you replace a piece of equipment?
- How much should you pay for it?
- Should you lease it?
- Should you trade it in?
- What about custom hire?
- Is your machinery cost per acre too high?
- Are your repair costs too high?
- Do you know what your annual ownership (fixed) costs are vs. operating costs?
- Buy new or used?
- How much of a downpayment should you have?
Items to Consider:
- Ownership Costs
- Depreciation
- Economic life
- Salvage value
- Hours and types of use
- Interest
- Capital recovery
- Net present value & discount rate
- Taxes (will vary by state)
- Insurance
- Facilities
- Depreciation
- Operating Costs
- Repairs & Maintenance
- How and where it is used
- Records and schedules
- Fuel and oil
- Labor
- Repairs & Maintenance
Resources:
These tools and resources will help you make informed equipment purchases to bring value to your business.
- Iowa State University Ag Decision Maker
- ISU Machinery Management Files
- Buying Used Machinery
- Replacement Strategies for Farm Machinery
- Estimating Farm Machinery Costs | Ag Decision Maker
- U of M Farm Machinery Management
As a farmer, your equipment is the backbone of your operation, and what you do today will determine the options you'll have tomorrow. Whether it's the trade-in value of your machinery or the balance you owe, there are a lot of factors to consider with machinery costs. It is important to surround yourself with the right people to navigate these decisions. SFB's Ag Team is ready to work with you on finding the right solution and position your operation for success.
*Data for the graph above is from WI, MN, IL & MI. FINBIN (2025). Center for Farm Financial Management: University of Minnesota. Retrieved from http://finbin.umn.edu (originally created March 24, 2025).
Brad Sirianni works out of SFB's Black River Falls office as part of our Ag Lending Team. Brad has a vast knowledge of farm analysis. He worked as a farm business production management instructor for a combined 16 years before joining SFB. Contact him at bsirianni@sfbank.com or 715-670-0729.